如何修复未完全固化的环氧树脂及紧急处理方案
作者:东莞华创发布时间:2025-03-16分类:胶粘知识浏览:196评论:0
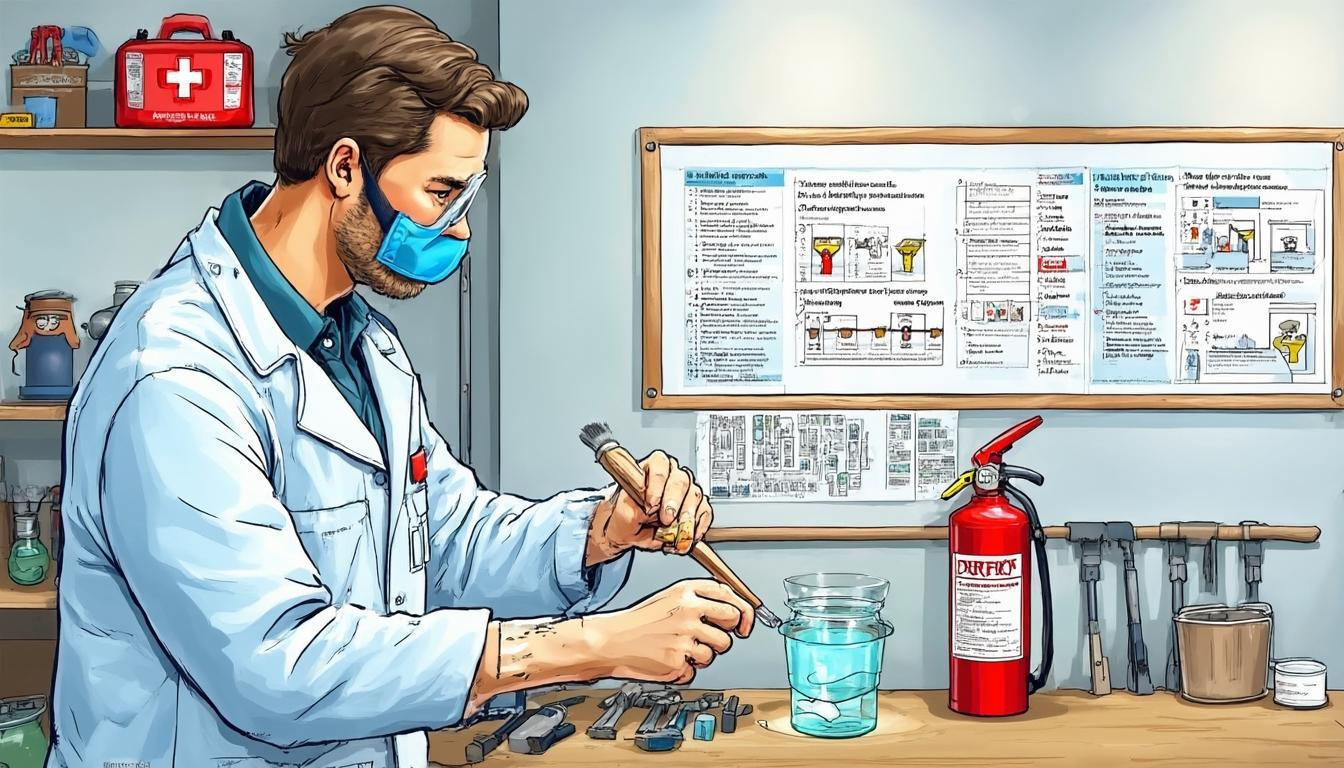
一、识别未完全固化的原因
环氧树脂未完全固化可能由多种原因造成,包括但不限于混合比例不当、固化剂使用错误、搅拌不充分、温度不适宜或着色剂添加过多等。在修复之前,要准确识别导致未固化的具体原因。
二、基本修复步骤
1. 检查混合比例:确保环氧树脂与固化剂的混合比例严格按照产品说明书进行,避免过量或不足。
2. 重新混合:如混合不均匀,需重新将环氧树脂与固化剂按比例混合,并充分搅拌至少3-5分钟,确保无气泡且混合均匀。
3. 调整温度:将工作环境和树脂温度调整至理想范围(75-85°F或24-30°C),以促进固化反应。
4. 延长固化时间:给予树脂更多时间进行固化,通常建议等待3-5天以达到完全固化。
三、针对特定情况的修复方法
1. 薄层树脂:对于较薄的树脂层,可能需要额外添加层数以增强固化效果,或使用坚固的底座以增强强度。
2. 着色剂影响:若着色剂添加过多导致固化不良,可减少着色剂用量至总体积的6%以下,并延长固化时间。
3. 灌封胶问题:对于灌封胶不固化或固化不完全的情况,需检查两个组分比例是否正确,以及是否混合均匀。
四、紧急处理方案
在发现环氧树脂未完全固化且存在安全隐患时,应立即启动紧急处理方案:
1. 迅速撤离:受影响人员需立即撤离现场,避免长时间暴露于可能有害的化学环境中。
2. 隔离区域:对可能产生污染的区域进行隔离,防止未固化的环氧树脂进一步扩散或造成环境污染。
3. 通知报告:迅速通知相关人员并启动应急预案,同时向相关部门报告情况,以便获取专业支持和指导。
4. 专业处理:在专业人士的指导下,对未固化的环氧树脂进行合理清理和处置,确保安全环保。
五、预防措施与后续跟进
为预防未来再次发生类似情况,建议采取以下措施:
1. 加强培训:对操作人员进行专业培训,确保其熟悉环氧树脂的混合比例、固化条件及安全操作规程。
2. 定期检查:定期检查设备和工具,确保其处于良好状态,避免因设备故障导致混合不均或固化不良。
3. 记录与分析:对每次使用环氧树脂的过程进行详细记录,并分析可能存在的问题和改进措施。
4. 持续跟进:对修复后的环氧树脂进行持续跟进观察,确保其达到预期的固化效果和性能。
- 上一篇:AB胶品牌环保性能排行及推荐
- 下一篇:固化剂的作用:环氧树脂胶的化学反应全解析
相关推荐
你 发表评论:
欢迎- 胶粘知识排行
- 标签列表